摘要:飛輪高強度螺栓在安裝時斷裂,斷口通過宏觀、電鏡掃描、能譜分析等均未發現異常現象,隨后進行微觀檢驗方法發現螺栓斷裂磨面有裂紋存在。故對裂紋來源進行了探究,結果表明斷裂螺栓磨面裂紋來源于在線切割制樣過程中運絲速度過快、冷卻液冷卻不充分、從而受熱導致裂紋產生。為避免以后裂紋的再次出現,建議將線切割機切割頻率參數調至合適的頻率、使用水基切削液、深磨試樣等方法。
關鍵詞:飛輪;高強度;線切割;深磨試樣
某公司是生產飛輪高強度螺栓的專業廠家,在安裝過程中出現規格為M10×1.25×28螺栓螺紋桿部發生斷裂現象。該斷裂螺栓材料為SCM440,機械性能等級為10.9級,硬度為39.0HRC-44.0HRC。該斷裂螺栓宏觀形貌見圖1。樣品螺栓在安裝時從螺紋桿部斷裂,扭力矩為91N·m。為查清螺栓斷裂磨面的原因,防止類似事件的發生,對斷裂螺栓進行了電鏡掃描,能譜及理化檢驗分析。
.jpg)
圖1 宏觀形貌及斷裂部位
1 理化檢驗
1.1宏觀檢驗
該螺栓斷裂于螺紋桿部,其斷口宏觀形貌見圖1。螺栓斷口垂直于軸線,整個斷口宏觀上可分為三個區:①斷裂源區,處于斷口的邊緣,螺紋根部。②放射區,為快速的斷裂區,呈現明顯的放射狀條紋特征,放射區面積較大,占斷口總面積的60%~70%。瞬間斷裂區,處于斷口的中心偏左,并與斷裂源呈45°角,這些特征表明該螺栓斷口為典型的在扭轉載荷作用下發生的混合型斷裂,以脆性斷裂為主。
1.2 斷口分析
運用EVO18掃描電子顯微鏡對螺栓斷口進行微觀形貌觀察和分析,電鏡下觀察斷口為撕裂準解理和韌窩狀塑性混合性斷裂(見圖2、3)。
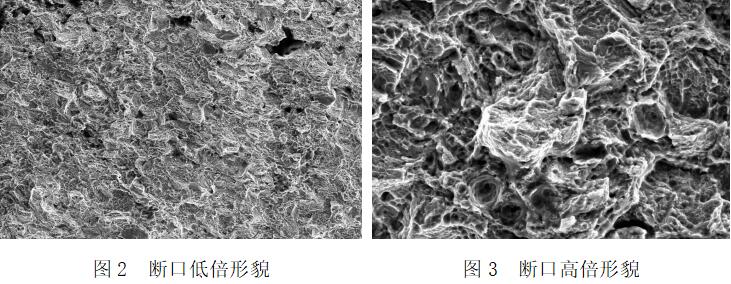
1.3 化學成分分析
運用MAXxLMM05直讀光譜分析儀進行化學成分分析,按(GB/T4336-2016 碳素鋼和中低合金鋼 多元素含量的測定 火花放電原子發射光譜法),結果見表1,可知螺栓的化學成分滿足協議SCM440的技術要求。
表1化學成分分析結果(質量分數)%
元素 | C | S | P | Mn | Si | Cr | Ni | Mo |
標準值 | 0.38~0.43 | ≤0.030 | ≤0.030 | 0.60~0.90 | 0.15~0.35 | 0.90~1.20 | ≤0.25 | 0.15~0.30 |
實測值 | 0.399 | 0.0070 | 0.0195 | 0.65 | 0.218 | 0.948 | 0.0208 | 0.197 |
1.4金相檢驗
對斷口進行縱向線切割,磨制、拋光后,制成金相試樣在光學顯微鏡下觀察,根據GB/T10561-2005/ISO4967:1998(E)實際檢驗A法,使用ISO評級圖評定,對鋼中非金屬夾雜物進行評級,斷裂螺栓的夾雜物級別為:硫化物類級別:0.5級(細系),氧化鋁類級別:0.5級(細系),硅酸鹽類級別:0.5級(細系),球狀氧化物類級別:1.0級(細系)。用體積分數為4%的HNO3 酒精溶液侵蝕后,用光學顯微鏡、掃描電鏡及能譜儀分析斷裂螺栓的顯微組織。在光學顯微鏡下觀察螺栓表層及芯部顯微組織均為正常的細小、均勻的仍保留針狀馬氏體形態特征的回火索氏體組織;組織中存在數條疑似裂紋形態現象,沿晶分布,(見圖4、5)。用掃描電鏡及能譜儀對疑似裂紋痕跡區域進行分析,痕跡區域成分主要為Fe、Cr、Mn元素,為基體組織內部正常元素,非外界物或者非金屬夾雜物質(見圖6、7、8、9、10、11和表2、表3)。
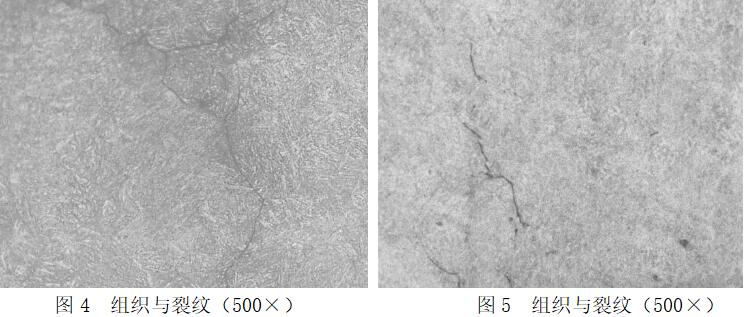
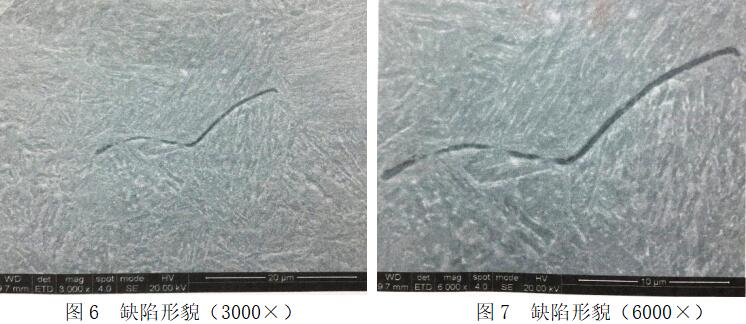
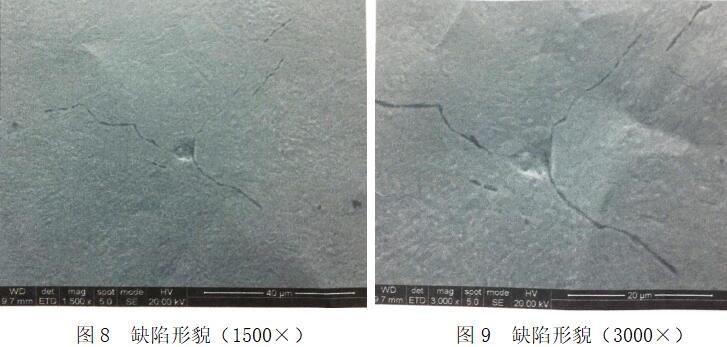
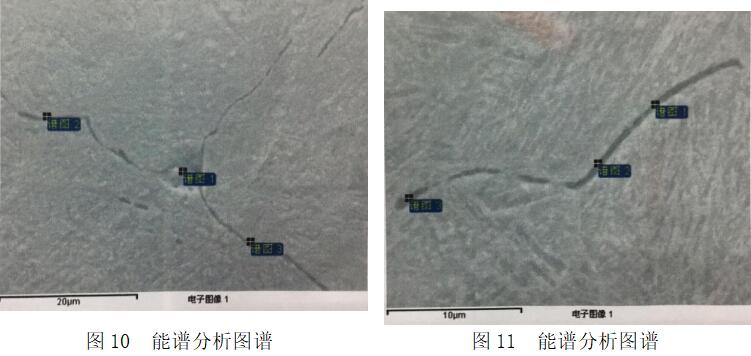
譜圖 | C% | Cr% | Fe% |
譜圖1 | 7.63 | 1.11 | 91.26 |
譜圖2 | —— | 1.17 | 98.83 |
譜圖3 | 7.91 | 1.25 | 90.84 |
譜圖 | C% | Mn% | Fe% |
譜圖1 | 1.32 | 2.17 | 96.51 |
譜圖2 | 1.04 | 1.48 | 97.47 |
譜圖3 | 1.06 | —— | 98.94 |
表2 能譜分析元素重量百分比表3 能譜分析元素重量百分比
將其掃描過分析的試樣磨面進行一次粗拋光和一次精拋光,試樣磨面的疑似裂紋均已經不存在(見圖12、13)。
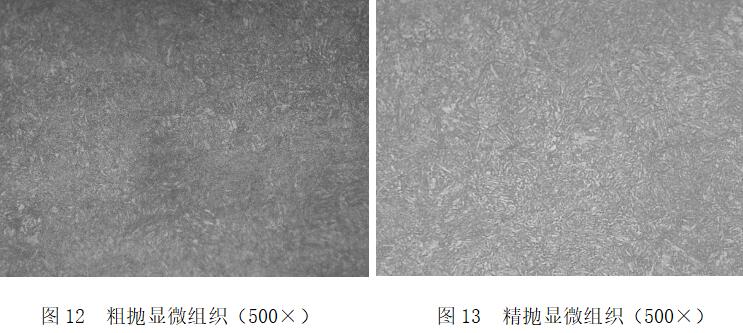
1.5硬度測試
用HR-150A洛氏硬度計對螺栓斷口橫截面,從螺栓表面至芯部進行硬度測試,其結果(見表4),結果顯示硬度較均勻,表面硬度在35.9HRC~37.3HRC范圍,平均值為 36.5HRC,芯部硬度為36.3HRC~38.3HRC,平均值為37.1HRC。
表4硬度測試結果
測試部位 | 實測值(HRC) | 平均值(HRC) |
表面 | 36.6 | 37.3 | 36.0 | 36.6 | 35.9 | 36.5 |
芯部 | 38.3 | 36.3 | 37.0 | 37.4 | 36.4 | 37.1 |
2 尋找裂紋來源
為探究斷裂螺栓磨面疑似裂紋來源,將裝機完好的螺栓抽取5件反復從人、機、料、法、環多方面進行分析驗證,具體驗證分析如下:
2.1 相同設備、相同人員、相同環境、不同方法下驗證
對1#螺栓采用原有線切割機進行縱向切割,原有人員進行金相制樣,改變磨樣方法,分四次逐層由表至里進行磨樣,拋光后用體積分數為4%的HNO3酒精溶液侵蝕后,用光學顯微鏡分析螺栓的顯微組織,觀察螺栓表層及芯部顯微組織均為正常細小、均勻的仍保留針狀馬氏體形態特征的回火索氏體組織;前三次磨樣都存在數條疑似網狀裂紋形態現象,沿晶分布。第四次未見疑似裂紋形態現象,見圖14、15、16、17。
2.2 相同設備、不同人員、相同環境、不同方法下驗證
對2#螺栓采用原有線切割機進行縱向切割,不同人員進行金相制樣,改變磨樣方法,分四次逐層由表至里進行磨樣,拋光后用體積分數為4%的HNO3酒精溶液侵蝕后,用光學顯微鏡分析螺栓的顯微組織,觀察螺栓表層及芯部顯微組織均為正常細小、均勻的仍保留針狀馬氏體形態特征的回火索氏體組織;同樣前三次磨樣仍存在數條疑似網狀裂紋形態現象,沿晶分布。第四次未見疑似裂紋形態現象,見圖18、19、20、21。
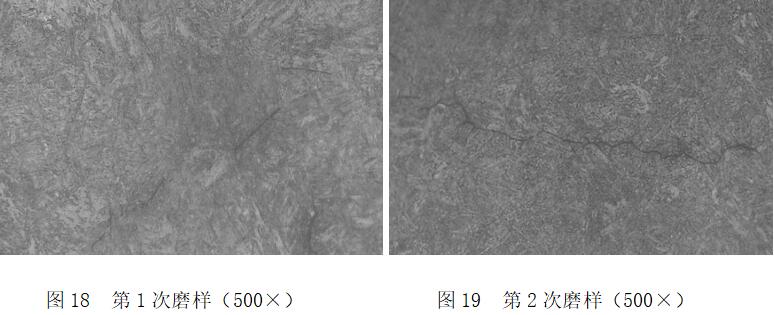
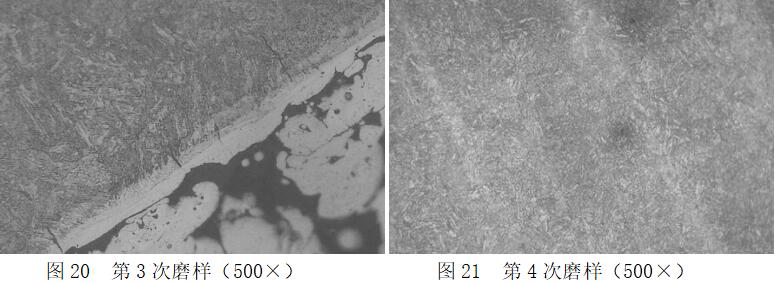
2.3 不同設備、相同人員、不同環境、相同方法下驗證
對3#螺栓采用不同實驗室線切割機進行縱向切割,由原有人員分兩次逐層由表至里進行磨樣,拋光后用體積分數為4%的HNO3酒精溶液侵蝕后,用光學顯微鏡分析螺栓的顯微組織,觀察螺栓表層及芯部顯微組織均為正常細小、均勻的仍保留針狀馬氏體形態特征的回火索氏體組織;未見疑似裂紋形態現象。見圖22、23。
通過對1#、2#、3#螺栓采用以上方法進行反復驗證后,發現不同線切割機之間切割頻率參數設置不一致、使用的冷卻液不一致。繼續對4#和5#螺栓進行驗證。
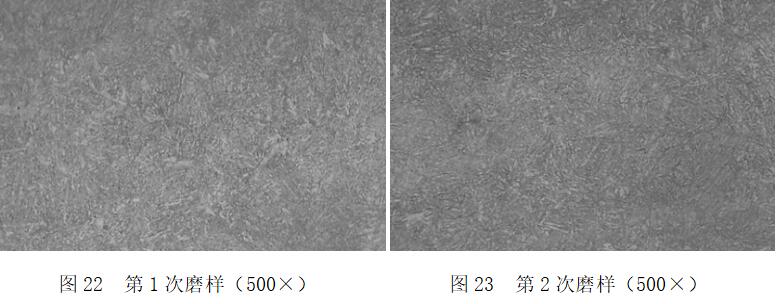
2.4 相同設備、相同人員、相同環境、相同方法下驗證
對4#螺栓采用原有線切割機設備,將切割頻率調至25Hz,更換冷卻液后進行縱向切割,原有人員進行金相制樣,分兩次逐層由表至里進行磨樣,拋光用經體積分數為4%的HNO3酒精溶液侵蝕后,用光學顯微鏡分析螺栓的顯微組織,觀察螺栓表層及芯部顯微組織均為正常細小、均勻的仍保留針狀馬氏體形態特征的回火索氏體組織;未見疑似裂紋形態現象。見圖24、25。
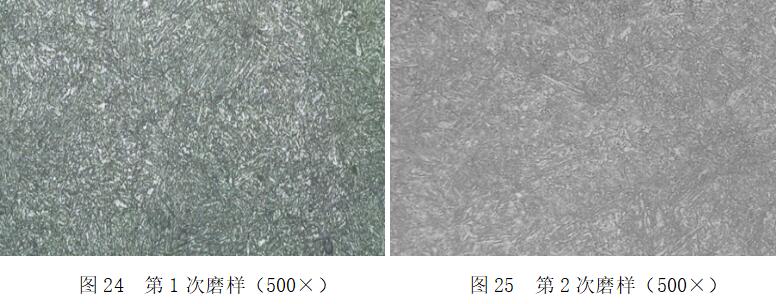
2.5 相同設備、不同人員、相同環境、相同方法下驗證
對5#螺栓采用原有線切割機設備,將切割頻率調至25Hz,更換冷卻液后進行縱向切割,不同人員進行金相制樣,分兩次逐層由表至里進行磨樣,拋光后用體積分數為4%的HNO3酒精溶液侵蝕后,用光學顯微鏡分析螺栓的顯微組織,觀察螺栓表層及芯部顯微組織均為正常細小、均勻的仍保留針狀馬氏體形態特征的回火索氏體組織;未見疑似裂紋形態現象。見圖26、27。
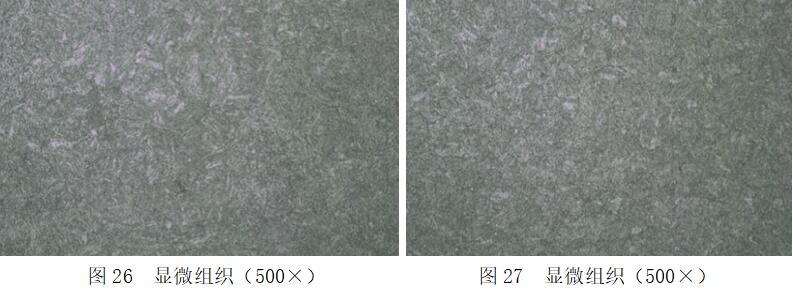
3 綜合分析及結論
(1)由于斷裂螺栓失效后,在做失效分析過程中發現螺栓斷裂面存在網狀疑似裂紋痕跡,能譜分析疑似裂紋痕跡區域成分為基體本身材質成分,非外來物質或者原材料本身的非金屬夾雜物。
(2)為探究斷裂螺栓磨面疑似裂紋來源,將裝機完好的螺栓抽取5件反復從人、機、料、法、環多方面進行分析驗證,樣品拋光腐蝕后疑似裂紋痕跡出現可有可無現象。由此可見,通過不同人員,不同設備,不同的制樣方法,不同的切削液反復驗證,總結得出,線切割機在切割時頻率過快,切削液不能快速冷卻,導致螺栓切面受熱,改變了組織,出現了表面微裂紋現象。
(3)為避免此類現象發生,建議將線切割機切割頻率參數調至合適的頻率、使用水基切削液、深磨試樣等方法。
參考文獻
[1]李炯輝主編金屬材料金相圖譜[M]北京機械工業出版社2006.6
[2]GB/T3098.1-2010緊固件機械性能 螺栓、螺釘和螺柱[S]
[3]鐘群鵬,趙子華.斷口學[M].哈爾濱工業大學出版社,2008